New REARM HR achieves high-level performance in asphalt concrete
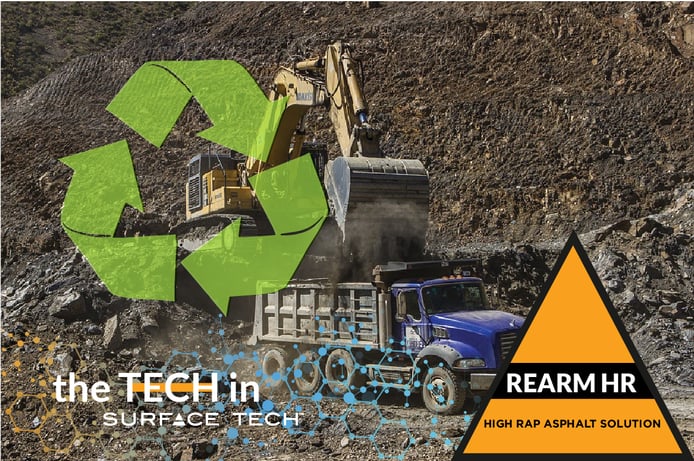
Poor performing mixes in the past have given RAP a bad rap, but Surface Tech and Georgia-Pacific Chemicals have developed a sustainable new mix design technology that can stand shoulder-to-shoulder with traditional lower RAP mixes in both crack and rut resistant performance tests.
By combining Surface Tech’s AQU Polymer Fiber™ and TUFFTREK 4007 from Georgia Pacific Chemicals, you can achieve up to 50 percent RAP usage and reduce the amount of virgin binder and aggregates in the mix. The REARM HR technology (formerly known as SMART RAP) also allows you to reduce the use of polymer modified binders.
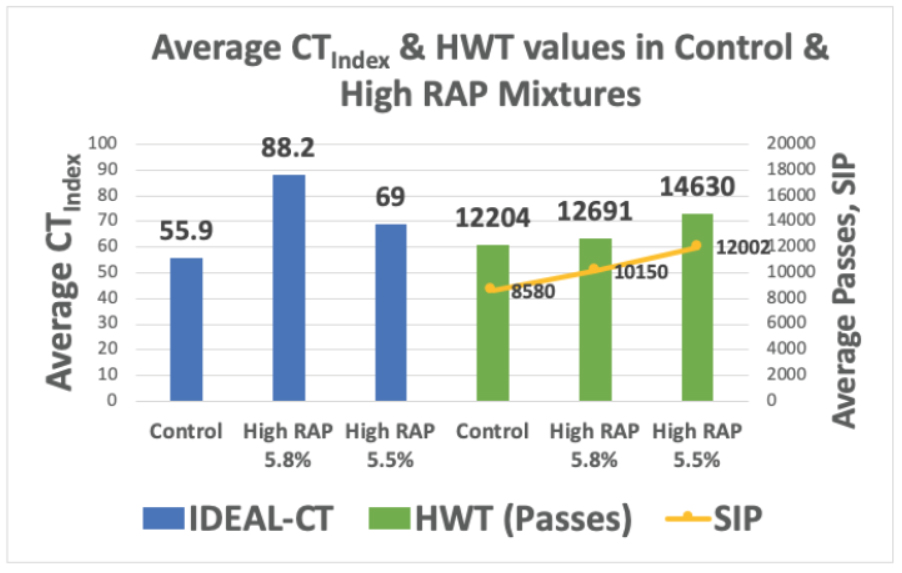
Best of all, you can chip away at those mountains of RAP, pave more roads at a lower cost and achieve an improved carbon footprint through recycling and lowering CO2 emissions. And you can kiss poor performance good-bye, thanks to the unique strengths of each product.
TUFFTREK 4007 is used to soften the virgin binder’s PG, which compensates for the addition of aged RAP binder. AQU Polymer Fiber™ reinforces the resulting combined binder with high strength 38mm aramid fibers. In lab tests, the IDEAL CT crack test (ASTM D8225) and the Hamburg Wheel Tracker rut test (AASHTO T324) demonstrate that REARM HR compares favorably to a low-RAP control mix.
Want to learn more? Give us a call. Let us partner with you to help reduce your stockpiles of RAP with a high-quality asphalt concrete mix you can count on — and that will give you important sustainable benefits.
For more information, contact us.