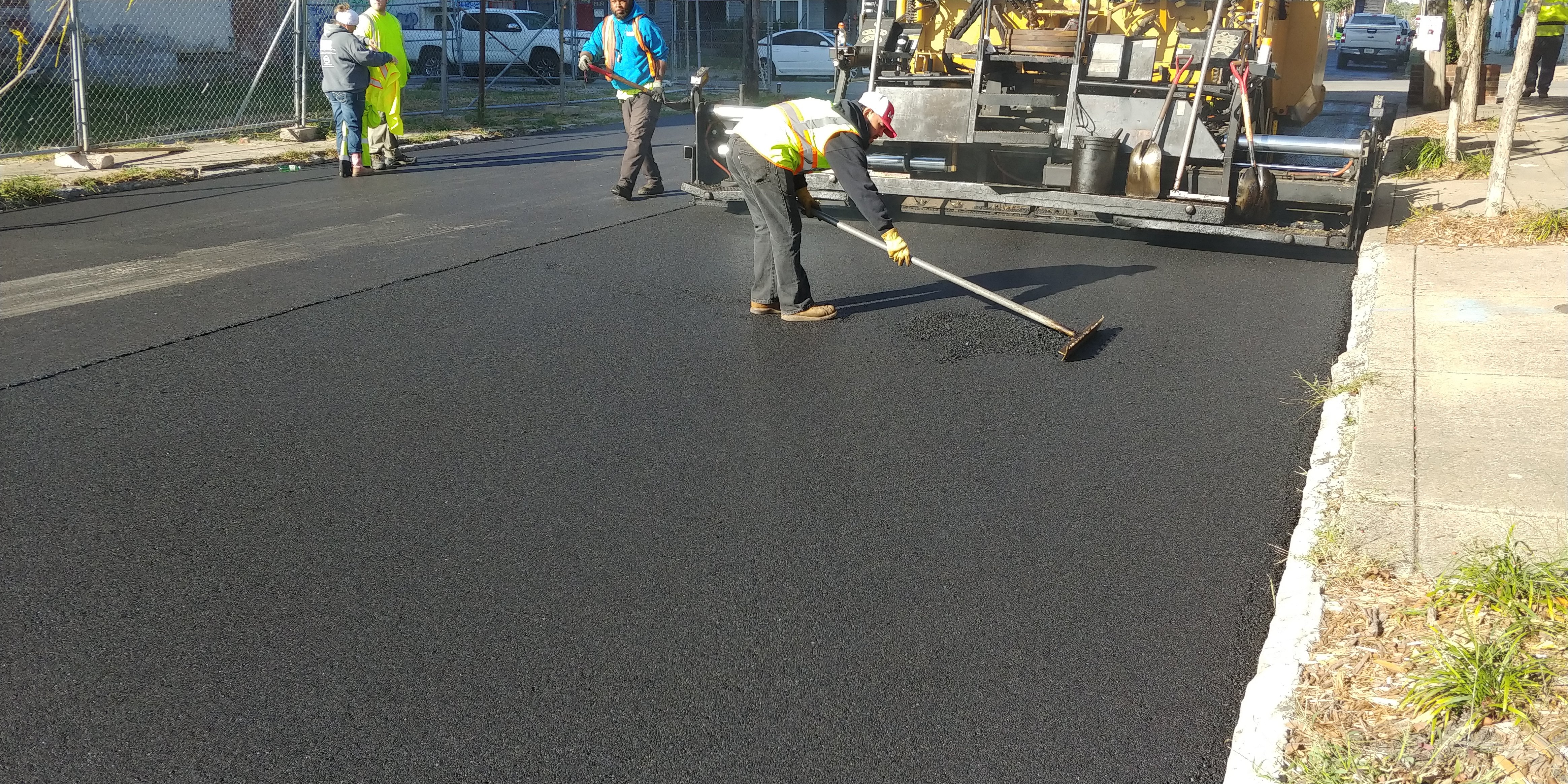
Hall Paving in Louisville, KY, recently discovered the sweet spot for using more RAP while keeping costs in line with traditional low-RAP pavement mixes. It’s a new development from Surface Tech called REARM HR™, the combination of a highly engineered bio-oil and aramid fibers that allows up to 50% RAP usage. This REAM HR™ project utilized the following in the 3/8” 5 NMAS; 5.6% PG64-22 total AC mix design:
Lampton Avenue Project — 10-14-2020
- 36% RAP (recycled asphalt pavement)
- TUFFTREK 4007
- ACE XP POLYMER FIBER™ from Surface Tech
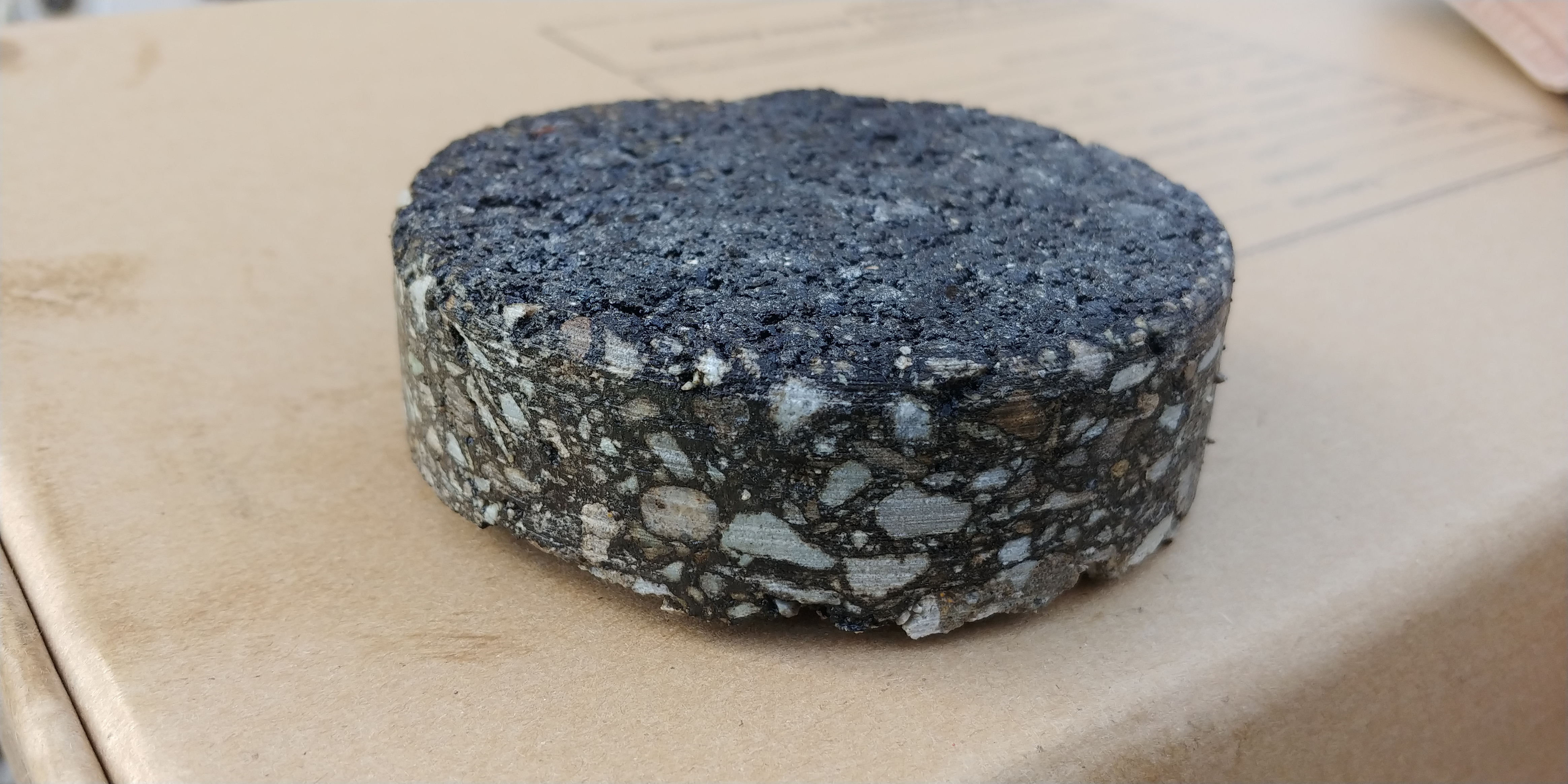
A total of 900 tons was produced for the three-mile project. Hall Paving succeeded in developing a mix design that added ACE XP POLYMER FIBER™ to every ton of asphalt at a neutral cost. The mix also increased the percentage of RAP over the standard 20% RAP design, while maintaining the cracking and rutting performance of lower RAP % mixes.
In addition to the RAP, TUFFTREK 4007 — a bio-oil from Bakelite — was introduced to soften the RAP and prevent brittleness. To add strength, REARM — an aramid reinforcement solution from Surface Tech — was added to the RAP/TUFFTREK mix. The bio oil allows for RAP to be added without the problem of over stiffening. Aramid reinforcement provides the rut and crack protection that is a must for a longer lasting solution.
ACE XP POLYMER FIBER™ aramid fibers strengthen the asphalt mix by providing increased tensile flexibility, which improves both cracking and rutting performance. TUFFTREK 4007 softens the virgin binder to compensate for the aged binder from the higher percentage RAP content. The resulting pavement resists rutting in hot weather and cracking through cold winters.
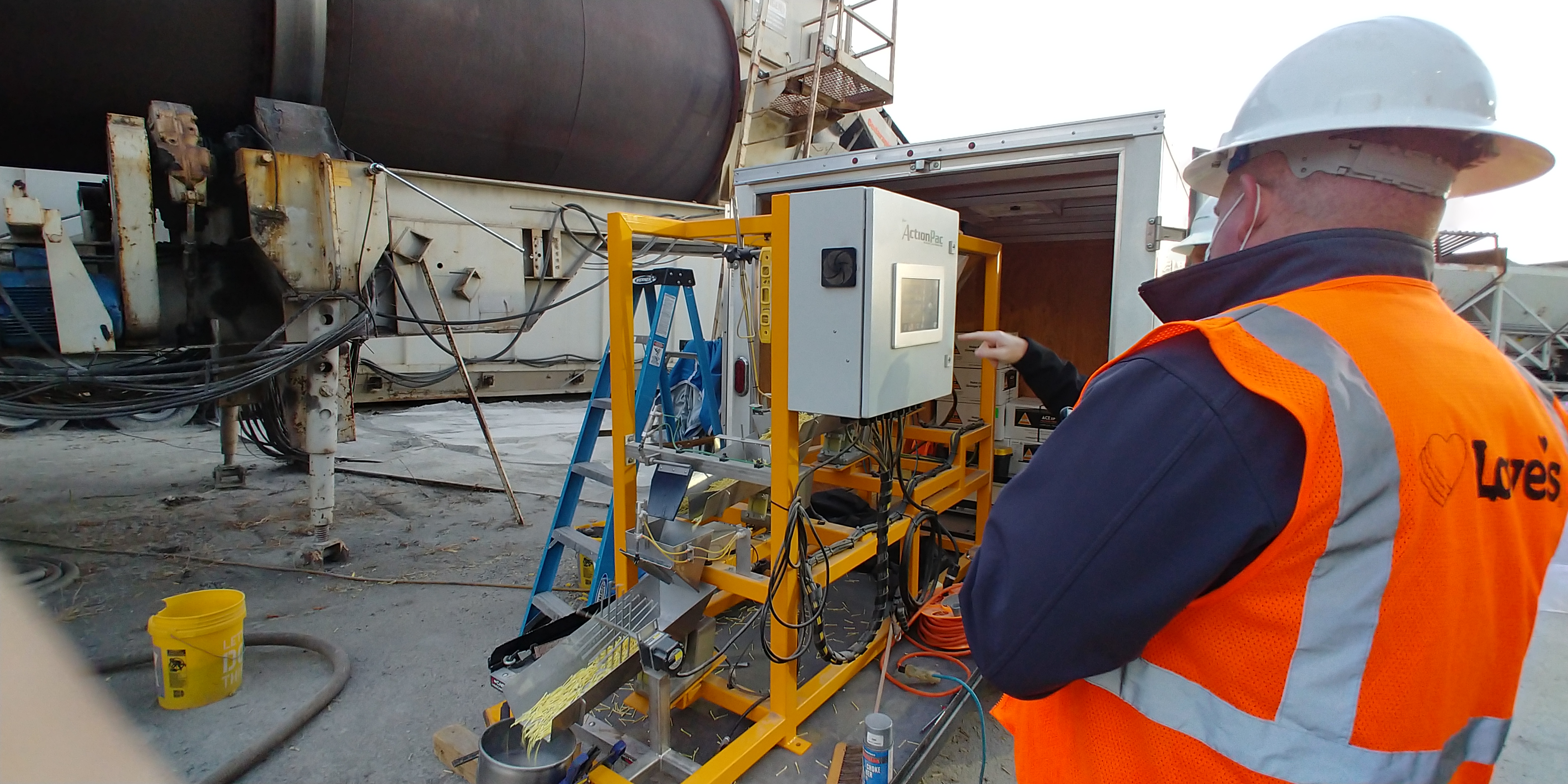
Final analysis: Pavement that lasts longer and requires less maintenance over its life span. In other words, the same up-front cost + lower maintenance costs = Big Win.
“Hall Paving was extremely excited about the way the mix went down and compacted,” said Joe Dennis, Surface Tech’s Chief Technical Officer for Asphalt. And the City was blown away by the look and performance going down. It’s really a smooth roadway.”
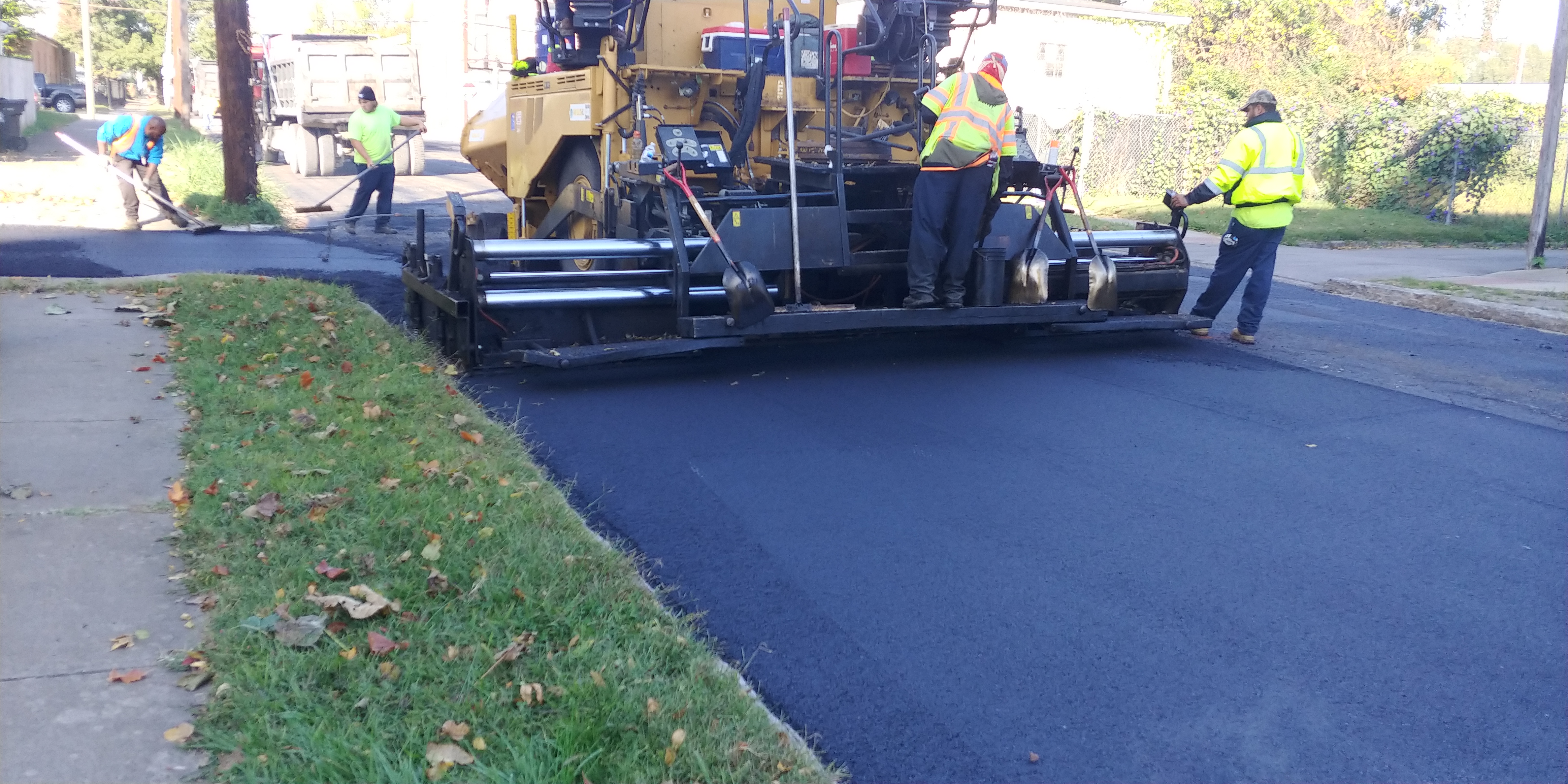
This mix was under the microscope! Blankenship Asphalt Tech and Training (BATT) assisted Surface Tech in testing and developing the successful formula and verified the mix with Hamburg Wheel Tracker and IDEAL-CT testing for rut and crack resistance. Surface Tech provided quality control support on site during production. S&ME was also on site to check overall quality on behalf of Louisville Metro.
Hall Paving used a pump system for adding TuffTrek 4007 from totes in line with the PG64-22 asphalt binder and dosed the ACE XP POLYMER FIBER™ into the HMA plant using Surface Tech’s Automated Micro Doser – MD3+. All parties agreed, the results were outstanding.
If you’re ready to increase the amount of RAP in your next project, plus get a tougher pavement at no extra cost, contact us.
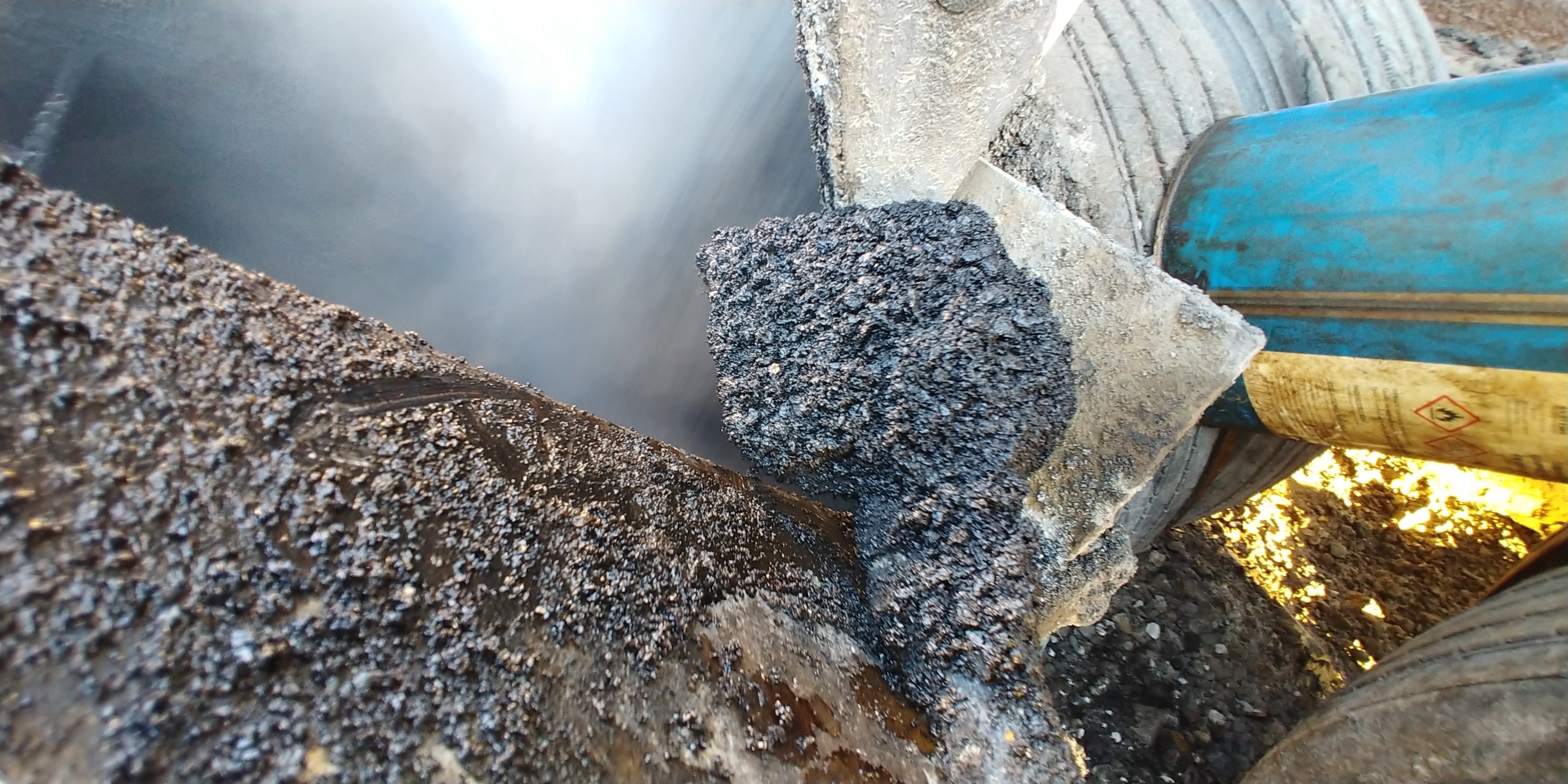
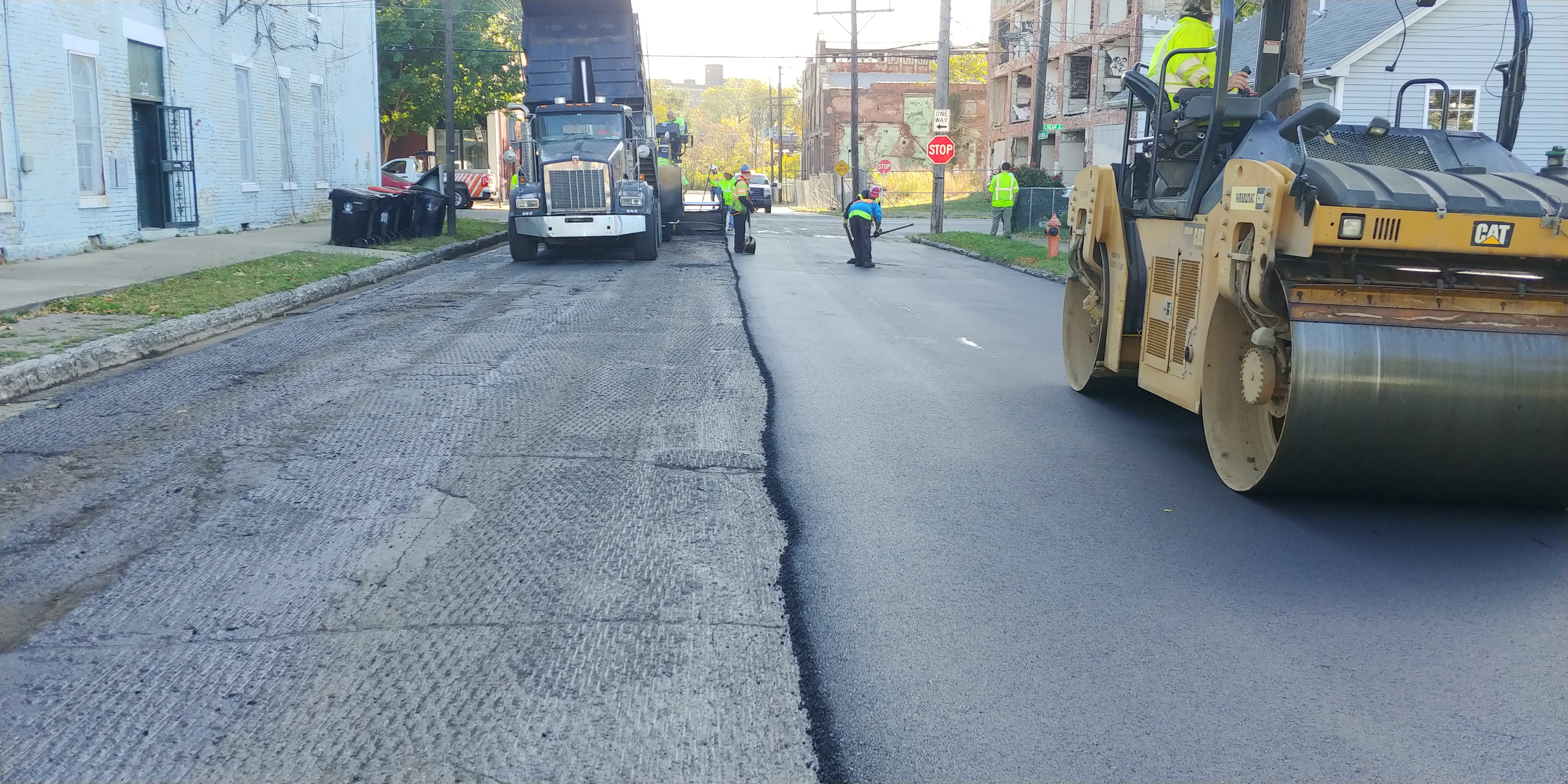